Making Tailstock Runners for a WW Lathe

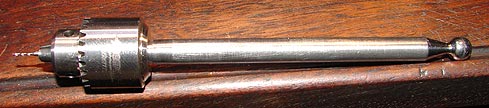
Copyright 2010 by James
P. Riser
This is the standard
tailstock on one of my WW lathes.
The knob on the right end has been removed for cleaning.
The left end has an internal taper for holding male
or female dead centers.
A collet holding adaptor may also be plugged into this
taper.
Such lathes have a rather short bed and using the collet
holding adaptor takes up too much space.
So I decided to make a couple more useful tailstock
runners. This web page documents the techniques I used to make
new runners.
Hopefully this information will be useful to others.
I started out by cutting a length of 5/16" air
hardening steel (A-2) for the runner.
W-1 (water hardening) or O-1 (oil hardening) steel
would also work.
After cutting to
length, the end was ground flat and slightly tapered.
I wanted to mount a new Jacobs Taper size 0 drill chuck
on the end of this runner for hand held drilling in the lathe.
This tiny taper
was to be ground on a Gorton tool grinder.
I looked up the proper angle and diameters for this
taper (1.4117 degrees). Small end is .2284". Large end is
.2500". Length of taper is .44".
It is impossible to just set the proper angle on my
grinder - so I chucked up a standard JT0 taper that I had and
set the angle from this.
After dressing the wheel, the next step was to begin
the actual grinding. The previously rough ground taper saved time.
A series of small ground flats was made to gently form
the proper taper. Below is a sequence of the various stages of
grinding.
This is the final grind for the taper.
After test fitting to the new chuck, the length was
shortened as needed and a slight chamfer ground on the end.
In use the runner slides within the tailstock and the
drill chuck is held by hand. This allows for very sensitive drilling
of small holes.
Here are the new
drill chuck and runner in use.
Drilling small
and larger holes.
The completed setup.
In addition I wanted a new dead center runner. This
runner was to be locked into position in the tailstock as needed.
The same grinder
was used, angle reset, and a series of flats ground.
These flats were then smoothed out into the new dead
center.
The final dead
center runner.
I am very pleased with the functionality of these two
new runners.
Click here to return to
my machinery page.